BSL-214
Automatische Horizontalschneidemaschine mit reversierendem Bandsystem zum Schneiden und Spalten von Platten verschiedenster Stärken
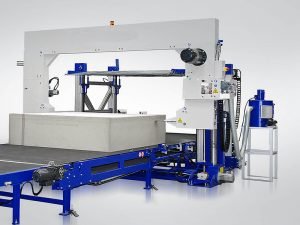
Horizontalschneidemaschine BSL-214
Zur Verarbeitung von leichten bis mittleren Raumgewichten
- Low throughput rates due to a maximum velocity of 80 m/min
- Effective increase in productivity
- Generation of optimal cutting angles and cutting of precise sheet thicknesses thanks to the all-automatic angle adjustment of the cutting unit
- Long knife lifetime and low set-up costs as the knife is relieved of the strain as it does not need to be turned due to the swivelling cutting unit
- Permanently high cutting precion throughout the knife lifetime thanks to the employment of a band knife of 30 mm width which is ground by an integrated grinding unit.
- Very precise cutting tolerances through high tensioning of the binding
- A perforated belt running around the table serves for the block transport and allows a fast and easy integration of the BSL-214 into automized production processes in connection with other cutting machines, e.g. an OFS-VS vertical contour cutting machine
Key Facts
Application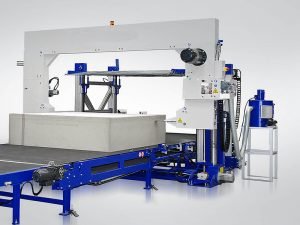
Möbel- & Matratzenindustrie, Automobil- und Fahrzeugindustrie, Verpackungsindustrie, Technische Artikel, Filterindustrie
Material
PU- Schaum und PU-Verbundschaum, Visco-Schäume, Basotect®, Latex, retikulierte Schäume
Cutting Tool
Die Maschine ist mit einem 30 mm breiten, endlosen Bandmesser ausgerüstet, das über 4 Räder im Aggregat läuft
Technical Data
|
Standard |
Options |
Block Width |
2 200 mm |
2 400 mm |
Block Height |
1300 mm |
1 500 mm |
Block Length |
3 050 mm |
2 600 mm |
Standard
- B-Con
- Schleifapparat
- Schleifstaubabsaugung
- Schnittwinkelverstellung durch motorisches Schwenken des Schneidaggregates von -1 bis +6°
- Vakuum
Options
- Mittenhalter für Bandage
- Be- und Entladebänder
- Höhenverstellbare Transportbahn
- Klimagerät
- Silikonsprüheinrichtung
Unloading conveyor
- Heightadjustable unloading conveyor
- Positioned downstream of the cutting unit of the BSL-214
- The unloading conveyor separates the cut or split sheets from the remaining block
- The height adjustable unloading conveyor separates the cut sheets (1 – n) from the remaining block and delivers them to the following transport conveyor
- By this function, single sheets as well as several sheets stacked onto each other can be removed for their subsequent converting. This function is often used e.g. in combination with our OFS-VS vertical contour cutting machine as this allows an excellent production process in a production line
- Is mainly used in cutting lines
- When integrated into a cutting line, a scissors lift provides for the sheet stacks to be delivered to the following converting machines.
- In order to cut sheet stacks with sheet thicknesses of more than 80 mm, the unloading conveyor can be pneumatically hoisted at its end which thus prevents a misalignment of the split sheets
Binding holder
- This option serves for an additional support of the cutting tool. For this, an aluminium holder is manually fixed to the binding which additonnally supports the knife.
- This option is essential for particularly heavy foams (e. g. rebond foam) or materials with a strain hardness of 7,0 kp or above
- Not feasible in connection with an unloading conveyor
Loading and unloading conveyors
- Optional equipment with loading and unloading conveyors
- Allow an automatic loading and unloading and thus a continuous production flow
- Positioned upstream or downstream of the machine
- Are mainly used in cutting lines
- Prevention of idle times of the machine
Spraying unit
- Wets the knife binding at intervals
- Minimization of frictional forces between the binding and the material to be cut
- Improved de-stacking performance
Table drive
- Option does not influence the cutting performance
- Necessary with a total block weight of more than 400 kg or a table length of 3 300 mm and above
- Reinforcement of the table drive
External vacuum
- In the working table there is a vacuum chamber which is connected to an external vacuum fan. This ensures that the material to be cut is correctly fixed during the cutting process
- More precise cutting results as the block is fixed and even the slightest shifting of the materail is prevented