BSV-EC
Splitting of bonded and separate long blocks (40-120 m)
BSV-EC long splitting machine
Most economic production of foil ware and best possible utilisation of the material: with foil thicknesses of 1 mm to 50 mm it is possible to wind a max. roller diameter of 1.5 to 2.4 m, depending on the corresponding machine version
- The long block to be split is continuously fed to the cutting portal by an endless transport system which is located in two reinforced semi-circular towers equipped with belt systems.
- Lowering of the cutting unit by the required foil thickness after each block cycle
- Zum Längenausgleich ist der Turm hinter dem Schneidaggregat motorisch verfahrbar
- For the reason of length compensation, the tower after the cutting unit can be moved by motor
- For a precise block guiding and for bonding the block, a motor-driven side guide is installed upstream of the cutting unit. The current position of the side guide is displayed on the operator panel.
- Clamp fitting in the towers enable the cutting of open blocks in semi-automatic circulation mode and the converting of long blocks of soft qualities
- Maximum cutting speed of 150 m/min with all versions and for all block lengths
- The maximum block weight with 60 m is 7 t
- The machine control is an efficient PLC by Siemens with a high operating convenience
- Storage of numerous cutting programmes and machines settings directly at the control panel
- Continuous, constant cutting result due to a programmable, all-automatic movement of cutting angle adjustment, pressure roller position and knife bar, in dependence on the foam quality
- Grinding cycles and the duration of the knife grinding can be pre-programmed.
- Continuous, high-quality grinding of the knife by a high-precision grinding unit with pneumatic advance of the cup wheels
Key Facts
Application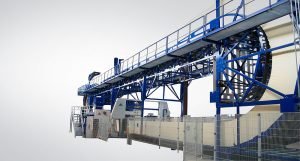
Automotive industry, mattress industry, footwear industry, apparel industry, packaging industrySplitting
Material
Polyether and Polyester soft foams with various densities and densities, rebond foam. Precondition: the flexible PUR soft foam used in the looper must be able to adapt itself to the radii of the deflection station without any difficulties. Long-splitting machine BSV-EC can process more flexible foams and higher densities than the BSV-E model.
Cutting Tool
Precision-ground circulating ground knife (width 80 mm, thickness 0.6 mm)
Technical Data
|
Standard |
Options |
Block Width |
2 300 mm |
2 500 mm |
Block Height |
1 300 mm |
1 500 mm |
Block Length |
40-120 m |
50 m, 60 m |
Standard
- Cooling unit
- Grinding dust extraction unit
- Grinding unit
- B-Con
- Motor-driven adjustable pressure roller
- Motor-driven adjustment of retainer
- Motor-driven cutting angle adjustment
- Motor-driven feeding bridge
- One side stop adjustable by motor
- Operation right hand
- Main transport conveyor with vacuum unit (extern)
- No winding unit
- 7 conveyor belt drives
Options
- Angle adjustable grinding discs 6-12°
- Quick change device for cup wheels
- Re-inforced grinding dust extraction unit
- Reversing mode for short blocks
- Reversing mode in connection with second feeding bridge
- Special lengths available on request
- Operation left hand
- Winding unit on separate lifting platform
- Troughed conveyor belt
- Circular cross cutter
- Catwalk
- Second side stop in trolley conveyor
- Strip cutter (outer trimming)
- Strip cutter with center cut (retractable)
- Ionization unit
- Antistatic brush
- Winding unit with supporting spindle
- Manual cone adjustment
- Cable numbering
- Frequency-controlled vacuum unit
Pressure roller
- Motor-driven pressure roller
- Necessary for the cutting of thin foils (1-5 mm) made from lightweight foam qualities (1-5 mm)
Third tower
- As a special version, the BSV-EC can also be equipped with a third tower
- By this, two different lengths of glued blocks can be converted, e.g. 60 m and 120 m
Winder
- Version A: Winding unit with 2 driven winding rollers; height adjustment effected using supporting spindles
- Version B: The winding unit consists of a belt system mounted on a moveable lifting platform. During the splitting operation, this automatically follows the cutting unit as the block height decreases. The operator stands on the lifting platform to ensure easy operation of the winding unit
Troughed belt conveyor
- The troughed conveyor is directly placed downstream of the winding unit
- Allows an easy removing of the completely wound foam roll from the machine to one side
Reverse mode
- Reverse mode in connection with the second feeding bridge
- For cutting long and short blocks made from materials which cannot be converted by a looper
- By this function, a long block which cannot or shall not be glued can be converted to roll ware
- Particularly for the cutting of heavy visco foams or similar materials
Circular knife cross cutter
- For economically cutting off the foils after they have reached the preset foil length
Cutting-off machine
- ABLG II for a straight and angular trimming of the head pieces before the long block is glued
- ABLG II S for a straight and angular trimming of the head pieces before the long block is glued. The cutting angle of the ABLG II S can be adjusted between 45 and 90 degrees. The angular cut of the ABLG II S guarantees a larger adherend particularly with foams which a difficult to convert.
- The set-up of the ABLG II and the ABLG II S is before the BSV-EC
IS-BA
- For an accurate lateral trimming of the long block
- Adjustment of the cutting units either by motor or manually by hand wheel
- Can be equipped with either a binding or a knife bar
ROK
- ROK Roll compression system for compressing and packaging polyurethane foam in roll form
- Compression and packaging of foam rolls for economic and space-saving storage and transport
- Reduction of the foam roll volume of up to 900 mm depending on foam type and machine specification
- For roll widths of 2 200 mm or 2 500 mm
- For roll diameters from 400-2 000 mm or 2 500 mm
- Belt speed of 20 m/min
- Up to 5 freely parameterizable compression and packaging programmes enable to an optimum coordination of the processes referred to different foam types
- Packaging foil is welded automatically when the number of entered wrap layers is finished